Kodiak CNC Plasma & oxyfuel Cutting
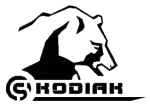
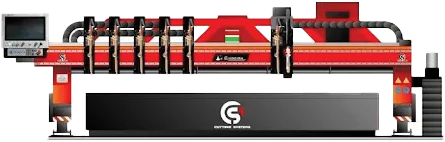
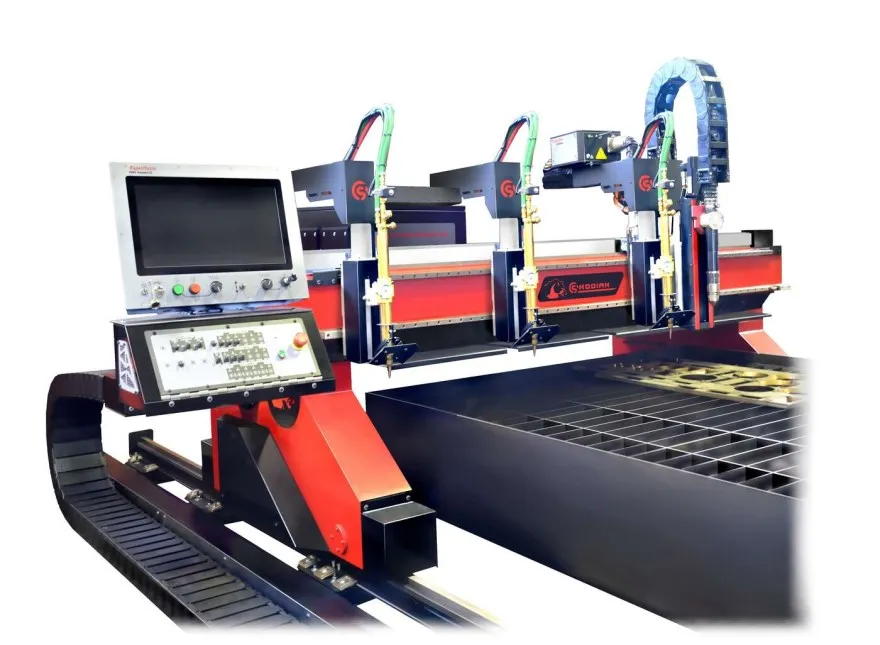
Quick Specs
- Cutting Process = Plasma & OxyFuel
- Cutting Widths = 6’ – 30’
- Cutting Lengths = 10’ – 250’
- Cutting Thickness = 6.25” Plasma, 24” Oxyfuel
- Hypertherm Plasma = 200 – 800 amps
- Oxyfuel = 1 – 12 Torches Standard
- Water/Downdraft Tables and Dust Collectors
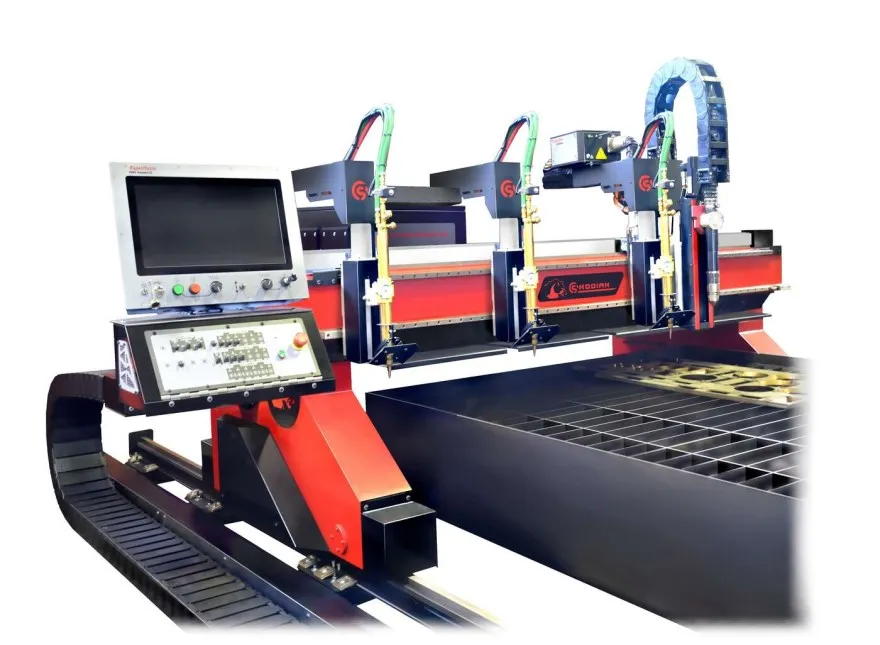
Product Description
The Kodiak CNC plasma and oxyfuel cutting machine delivers industrial-grade cutting performance with customizable configurations for plasma and oxyfuel applications. It features a sturdy, solid steel bridge, powerful Yaskawa servo drives, and an advanced Hypertherm CNC motion control system.
MADE IN THE USA: The Kodiak CNC plasma and oxyfuel cutting machine is a high-precision system built to handle demanding cutting tasks across a variety of industries, from heavy equipment manufacturing and steel fabrication to mining and automotive production.
Standard Equipment
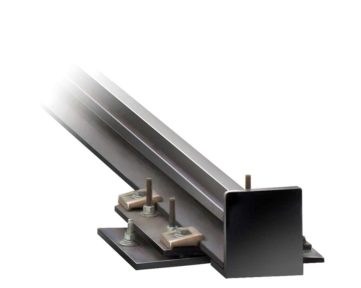
Industrial Strength Construction
Constructed with fully machined and welded beams and end trucks, Kodiak’s solid steel structure ensures durability and longevity, even in harsh industrial conditions.
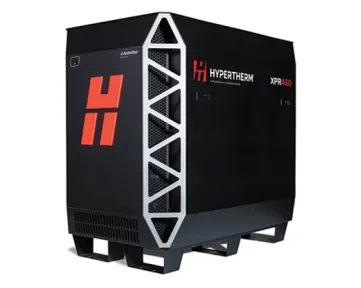
Hypertherm Plasma and Harris Oxyfuel Torches
Equipped with Hypertherm plasma power supplies, Sensor THC, and Harris oxyfuel torches with motorized lifters for reliable performance and superior cutting accuracy.

Yaskawa Drive System
Kodiak Cutting System with Hypertherm CNC Controller
The Kodiak Cutting System is built for heavy-duty industrial cutting and easily handles thick materials. When paired with the Hypertherm CNC Controller, it becomes a fully automated cutting solution, perfect for high-volume production and precision tasks.
How the CNC Controller Enhances the Kodiak
- Automated Cutting: The CNC Controller allows the Kodiak to perform difficult cuts with very little operator input, perfect for industries like shipbuilding, structural steel, and heavy fabrication.
- Precision and Consistency: The CNC controller ensures that every cut is accurate and repeatable by controlling parameters like amperage, gas flow, and cutting speed.
- Seamless Integration: The controller works with CNC tables, making it easy to automate cutting processes and improve efficiency.
- Real-Time Monitoring: The CNC Controller tracks system performance, alerting operators to issues like consumable wear or gas pressure drops, reducing downtime.
- Easy Programming: The intuitive interface simplifies setting up cutting programs, allowing operators to switch between jobs quickly.
Lower Maintenance = High Performance
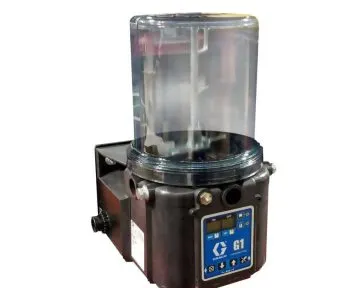
Automatic Lubrication System
With automatic lubrication of linear ways and bearings, Kodiak requires minimal maintenance, reducing downtime and keeping your operations running smoothly.
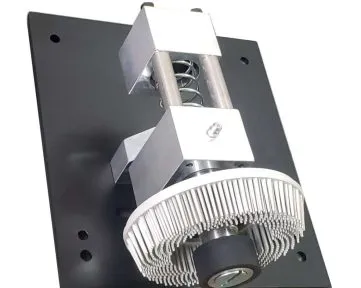
Automatic Rail Scrubbers
Kodiak includes proprietary automatic rail scrubbers that help maintain clean rails, reducing maintenance needs and increasing the system’s operational life.
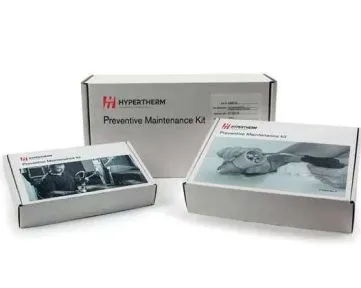
Preventative Maintenance Kits
For optimal performance, Kodiak provides preventative maintenance kits with essential parts installed at timed intervals to keep your machine in peak condition.
Engineered to Order
Kodiak offers a range of configuration options, including custom bridge widths up to 30 feet, multiple torch stations, and various plasma and oxyfuel torch setups. Whether you need an I-beam rail system, adjustable torch spacing, or laser alignment pointers, Kodiak’s versatile design can be tailored to meet your unique cutting application needs.